Our Process
Let’s see how we would work on a project or product, lorem ipsum dolor sit amet, consectetur adipiscing elit. Suspendisse id quam tortor.
- Home
- Our Process
We Work Strictly And Rigorously!
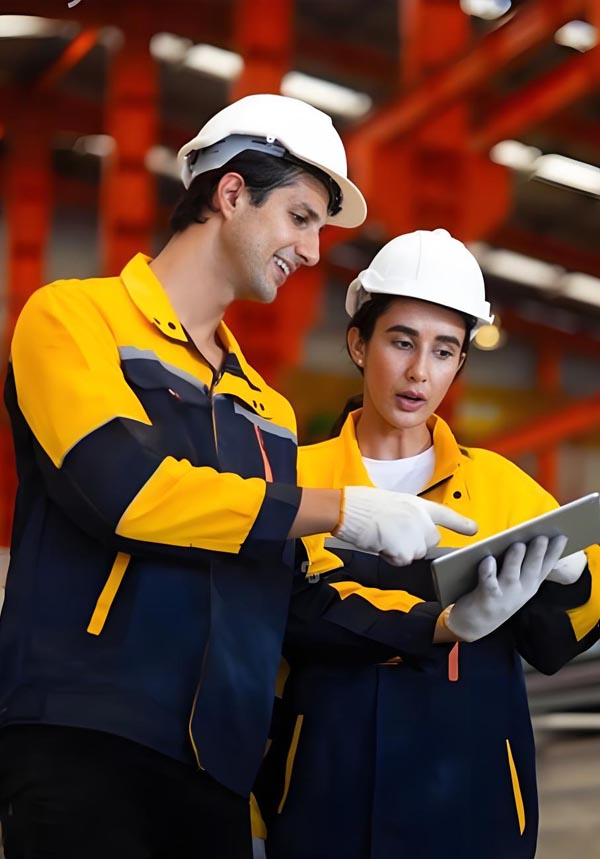
Step 1: Conceptual Design with Purpose
Overview: The journey begins with a spark of inspiration—understanding the client’s vision and translating it into a machine that can shape metal with surgical precision. This stage is where engineers, driven by curiosity and problem-solving zeal, lay the groundwork for a machine that will endure years of relentless operation.
Client Collaboration: Engineers immerse themselves in the client’s world, grasping the nuances of their needs—whether it’s forming high-strength steel for skyscraper beams or delicate aluminum for solar panel frames. This dialogue shapes specifications like profile complexity, production speed (e.g., 20–60 m/min), and material tolerances.
3D Design with Soul: Using advanced CAD tools like SolidWorks or CATIA, designers craft detailed 3D models, breathing life into components like roll stands and drive systems. Every curve of a roller is meticulously planned to guide metal smoothly through its transformation.
Stress Analysis with FEA: Finite element analysis (FEA) becomes the crystal ball, predicting how components will behave under the punishing forces of continuous operation. Engineers simulate stress, strain, and deformation, ensuring rollers and frames can withstand years of service without faltering.
Roll Tooling Artistry: Designing the rollers—the heart of the machine—is akin to sculpting. Specialized software like COPRA optimizes the forming sequence, minimizing material stress while achieving pinpoint accuracy. Each roller set is a bespoke creation, tailored to the unique profile it will shape.
Emotional Resonance: This stage is where dreams take shape. Engineers pour their expertise and creativity into designs, knowing their work will enable industries to build safer buildings, faster cars, and greener energy solutions. It’s a labor of love, grounded in the physics of mechanics and the thrill of innovation.
Step 2: Crafting Components with Care
Overview: With the blueprint in hand, the focus shifts to crafting the machine’s components—rollers, frames, shafts, and gears—with the precision of a watchmaker and the durability to withstand industrial demands. This stage is where raw materials are transformed into the building blocks of a masterpiece.
Production Techniques:
Material Selection with Intent: Materials are chosen with reverence for their properties. Rollers demand high-carbon tool steels (e.g., D2, HRC 60) for their wear resistance, while frames rely on robust structural steels like Q345 to absorb vibrational forces. Every choice is a balance of strength, toughness, and longevity.
Precision Machining: CNC machines hum with purpose, carving rollers and shafts to tolerances as fine as ±0.005 mm. Surface finishes are polished to mirror-like perfection, ensuring metal sheets glide through without a scratch.
Heat Treatment Alchemy: Rollers undergo quenching and tempering to achieve a hardened surface with a tough core, capable of enduring abrasive materials like galvanized steel. Induction hardening may be used for localized strength, a process rooted in metallurgical precision.
Protective Coatings: Chromium or ceramic coatings are applied to rollers, shielding them from wear and corrosion. This is not just protection—it’s a commitment to longevity, ensuring the machine thrives in harsh environments.
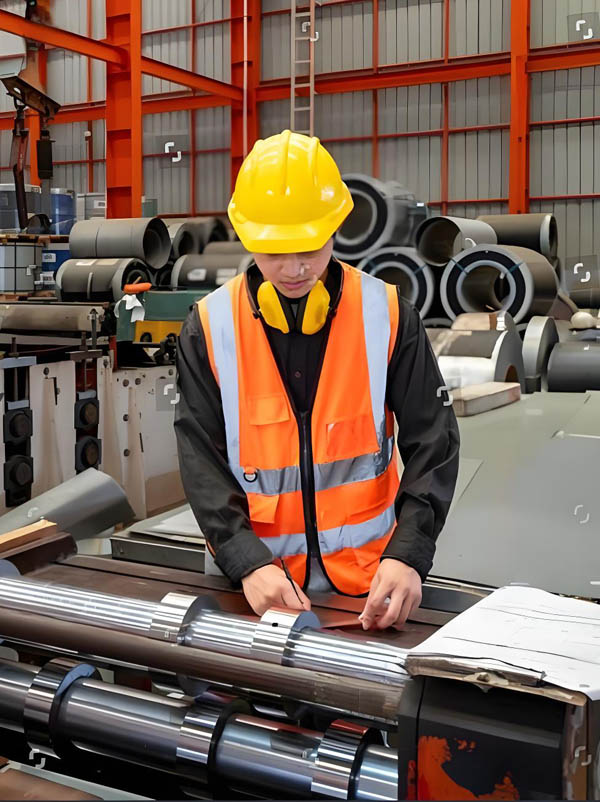
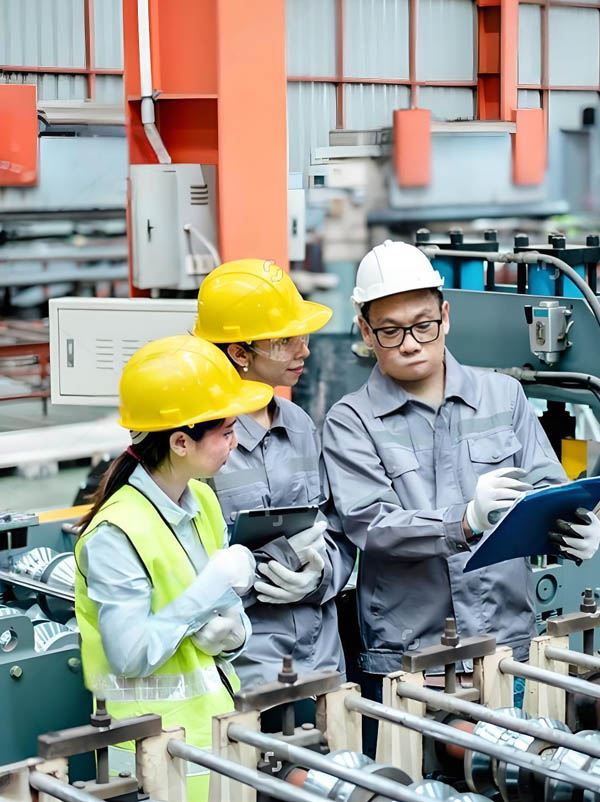
Step 3: Inspection And Testing
Production Techniques: Frame Construction: The machine’s skeleton—its frame—is welded or bolted with laser-guided precision to ensure perfect alignment. Misalignment by even a fraction of a millimeter could disrupt the forming process, so every joint is crafted with care.
Roller Installation: Rollers are mounted onto shafts with exacting precision, using shims and spacers to fine-tune gaps. This ensures uniform pressure across the metal sheet, preventing defects like warping or buckling.
Drive System Synergy: Servo motors or AC drives are paired with precision gearboxes, delivering power with finesse. Chains or belts are tensioned to perfection, ensuring smooth, synchronized motion.
Smart Control Integration: PLCs or CNC systems are wired into the machine, acting as its brain. Touchscreen HMIs are installed, offering operators intuitive control over speed, pressure, and cut-off operations.
Lubrication and Cooling: Automated lubrication systems keep friction at bay, while cooling systems—whether air or water-based—dissipate heat from high-speed forming, ensuring consistent performance.
Step 4: Rigorous Validation Through Testing
Production Techniques:
Dry Run Trials: The machine is powered on without material, allowing engineers to observe its rhythm—motor hum, roller spin, and control system response. This is the first test of its mechanical soul.
Material Forming Tests: Sample sheets of steel, aluminum, or copper are fed through the machine, producing profiles that are scrutinized for accuracy and surface quality. This is where theory meets reality.
Stress Endurance: The machine is run at maximum capacity, simulating months of operation in hours. This tests its resilience under high-speed, high-load conditions.
Calibration Precision: Sensors and controls are fine-tuned to ensure parameters like forming speed and cut-off length are razor-sharp, delivering consistent results.
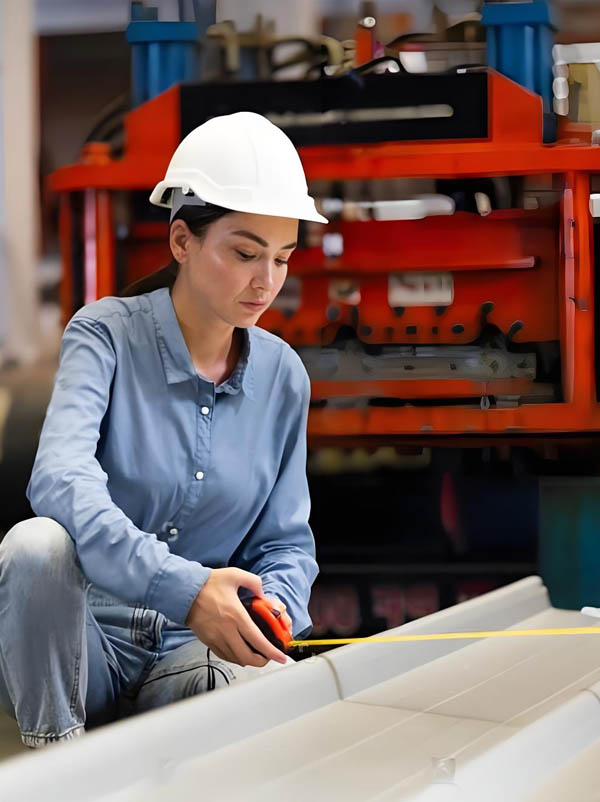